Business
Mining automation to be more prevalent in 2017
Mining automation was worth $5.98 B in 2014. The market is set to rise $22.59 B by 2024. It will be the trigger for the mining industry’s transformation.
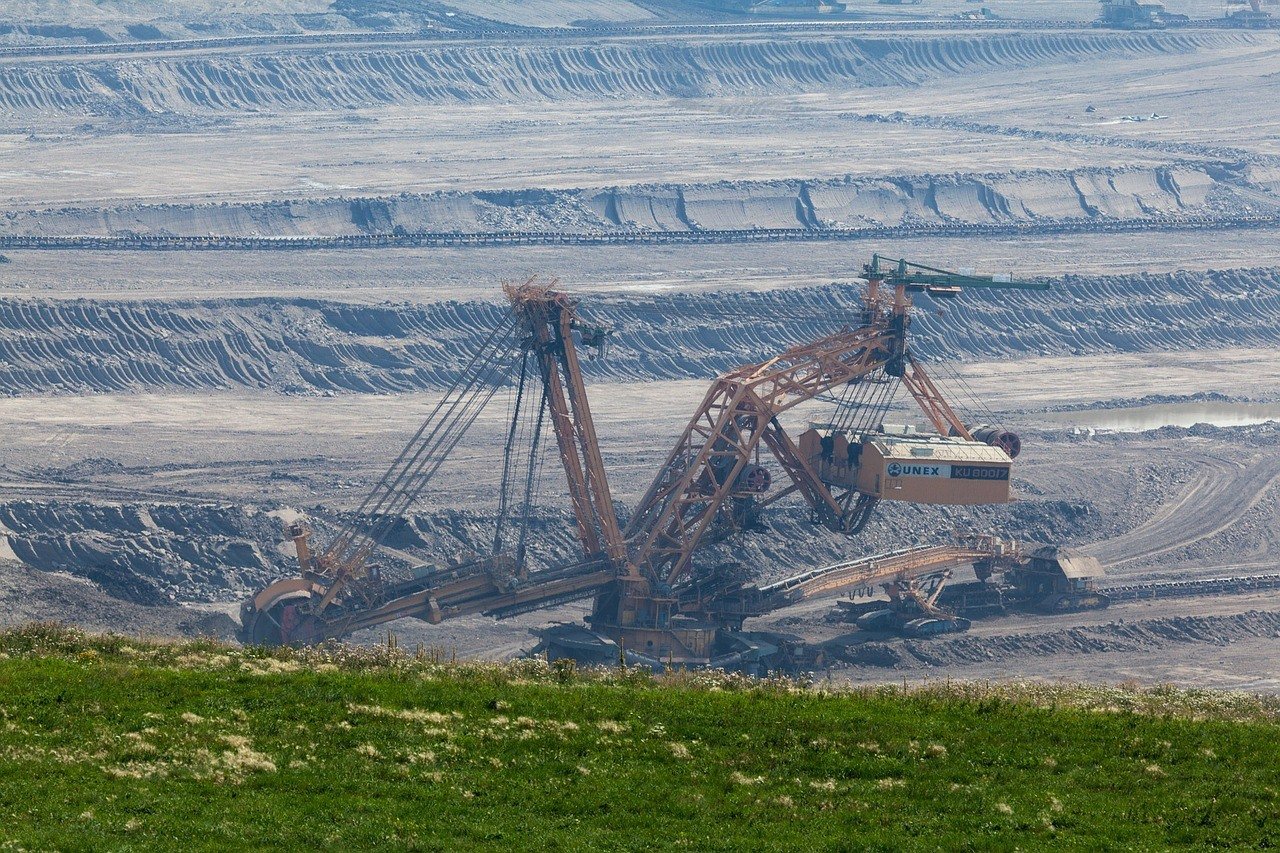
The latest McKinsey Global Institute report, published this January, reveals that most of the tasks today can be done with the currently available technology. The report also stated that automation will change the way work is done in many industries, mining included. Australian Mining further indicates that the smart mining industry is set for a “boom.”
This claim is backed up Transparency Market Research’s study released last November 2016, which said that the smart mining market is bound for growth in the coming years. The global smart mining market was assessed to be worth US$5.98 billion in 2014. By 2024, the market is projected to climb up to US$22.59 billion. Furthermore, it cites the introduction of mining automation and smart mining technologies in production as the trigger for the global mining industry’s transformation.
The mining industry is now embracing automation in its processes. According to GineersNow, this shift is a response to the need to reduce mining costs while increasing efficiency and quantity in production. A 2015 study from Mining Journal reported that the demand for industrial automation and control systems, equipment control, updated mine-surveying technologies, and simulator training increased during the past decade.
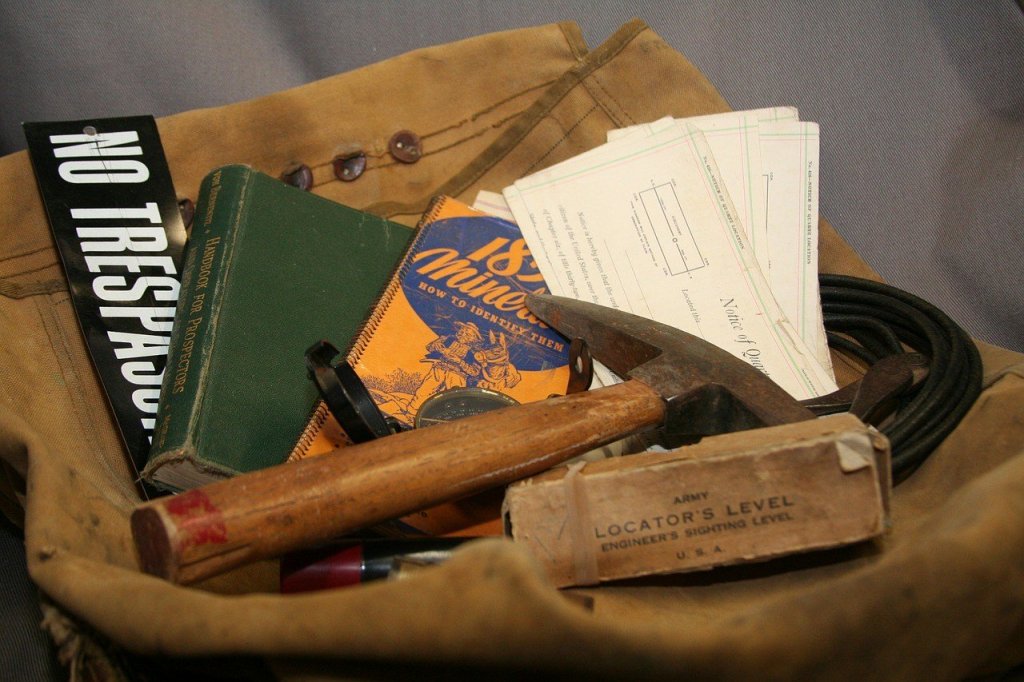
Mining automation will be a bigger part of the industry for 2017. (Source)
Why automated mining?
Smart mining technologies can be seen in two aspects: software and process automation and automated control on mining equipment.
In a publication by EY (formerly known as Ernst & Young), productivity is listed in the third spot of the top 10 business risks faced by mining and metals. The publication detailed that miners are struggling to improve in this area, especially in assets productivity.
With the aid of the automated production management software, delays and problems will be kept to a minimum. Monitoring and management can be organized more efficiently. If there are problems encountered, contingency plans are easier to carry out. Some companies, like Swedish mining corporation Sandvik and Pennsylvania-based software development company Bentley, offer production management and software solutions for mining companies to use. Sandvik’s production management software provides mining companies with real-time data of production delays and problems, allowing the management to make immediate corrective action to address the issues.
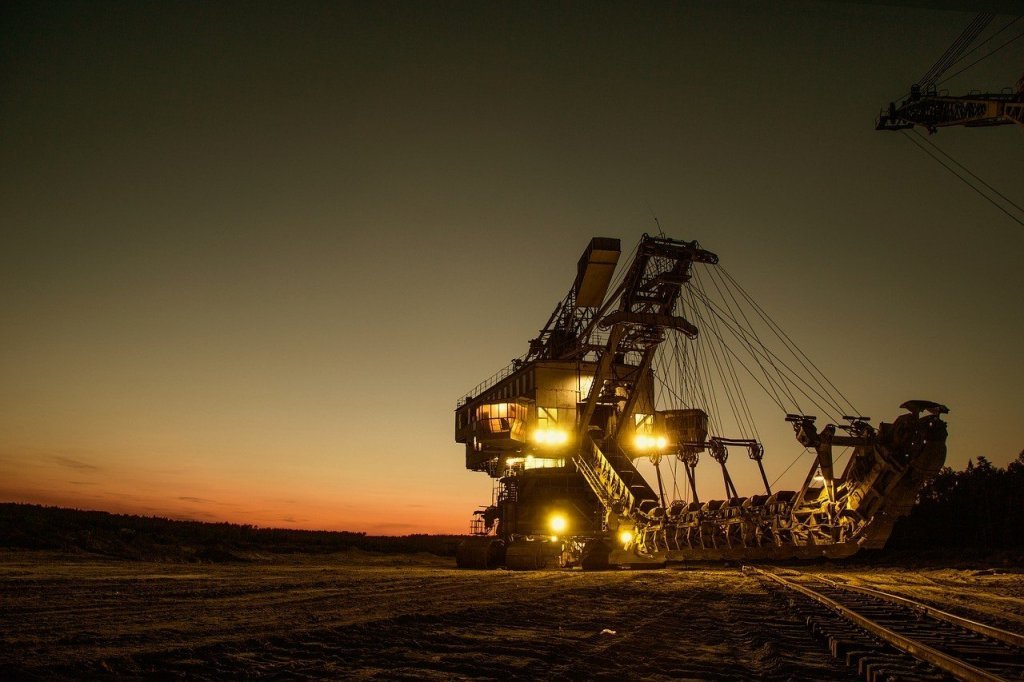
The raw minerals industry will see more mining automation technologies. (Source)
On the other hand, mining automation will also emphasize the improvement in the production quantity and quality without compromising the safety of the miners. Once automated, transport crawlers, bucket-wheel excavators, surface drilling equipment and mechanical cutting machines will speed up the daily mining process while extracting more minerals than usual.
Automatic control also allows remote monitoring for miners. This especially helpful in ensuring the workers’ safety during dangerous processes like blasting and drilling. The miners can look on in a safe distance or in control rooms while operating the computerized equipment.
However, machines replacing the human workforce from the mining process can create a ripple of effects not only in the mining industry but also in the labor industry, as the employment of some miners is, inevitably, on the line.
Raw minerals, economy, and environment
Mining automation has also made its way in the raw minerals industry. Russian company World of Diamonds Group uses automated systems installed with infrared detectors over conventional crushers. They use this for the primary crushing process that expands the size of diamonds surviving the recovery process—without compromising the quality of the stone,
Raw mineral firms taking on automated technologies will not only reap the benefits mentioned in the earlier section but will also be more flexible. In Mining Review Africa’s interview with Dr. Gordon Smith, Anglo American Platinum’s executive technical head, the mining industry will gain more flexibility when it comes to determining a mine’s layout.
If an automated equipment update is done, mining companies can alter the design of the mines and streamline their operation and production will be more flexible. Consequently, the mines will also become more adaptable in various economic conditions.
According to Mainland Machinery, automation will also reduce not just the health hazards for workers but also the environmental destruction brought about by mining base metals and raw minerals. The greater control over the production which automated equipment give, the bigger opportunity and the more time there is for to accurately assess their impact on the environment. It even paves way for the industry firms to develop ways and methods to lessen or, better yet, eliminate the detrimental effects on nature their explorations and drillings might have.
As technology advances with time, companies adapt their methods to keep going. For the mining industry to remain alive, its players must similarly adapt to the changes and update their equipment to keep the production going, to address health, safety, and environmental concerns, to improve low output and to have a greater control over the quality of the minerals produced and extracted from the earth.

-
Markets2 weeks ago
The President, The Fed, and the Fragile Foundations of Economic Trust
-
Business2 days ago
The TopRanked.io Weekly Digest: What’s Hot in Affiliate Marketing [Gambling Affiliation Review]
-
Business6 days ago
Debt-Fueled Highs: Dow Jones Stalls as Gold Signals Market Shift
-
Fintech4 days ago
Qubic’s Alleged 51% Attack: From Monero to Dogecoin Targets
You must be logged in to post a comment Login