Business
Reduce manufacturing energy costs in 6 simple steps
Manufacturers tend to consume a lot of energy for their production, resulting in steep costs in electricity.
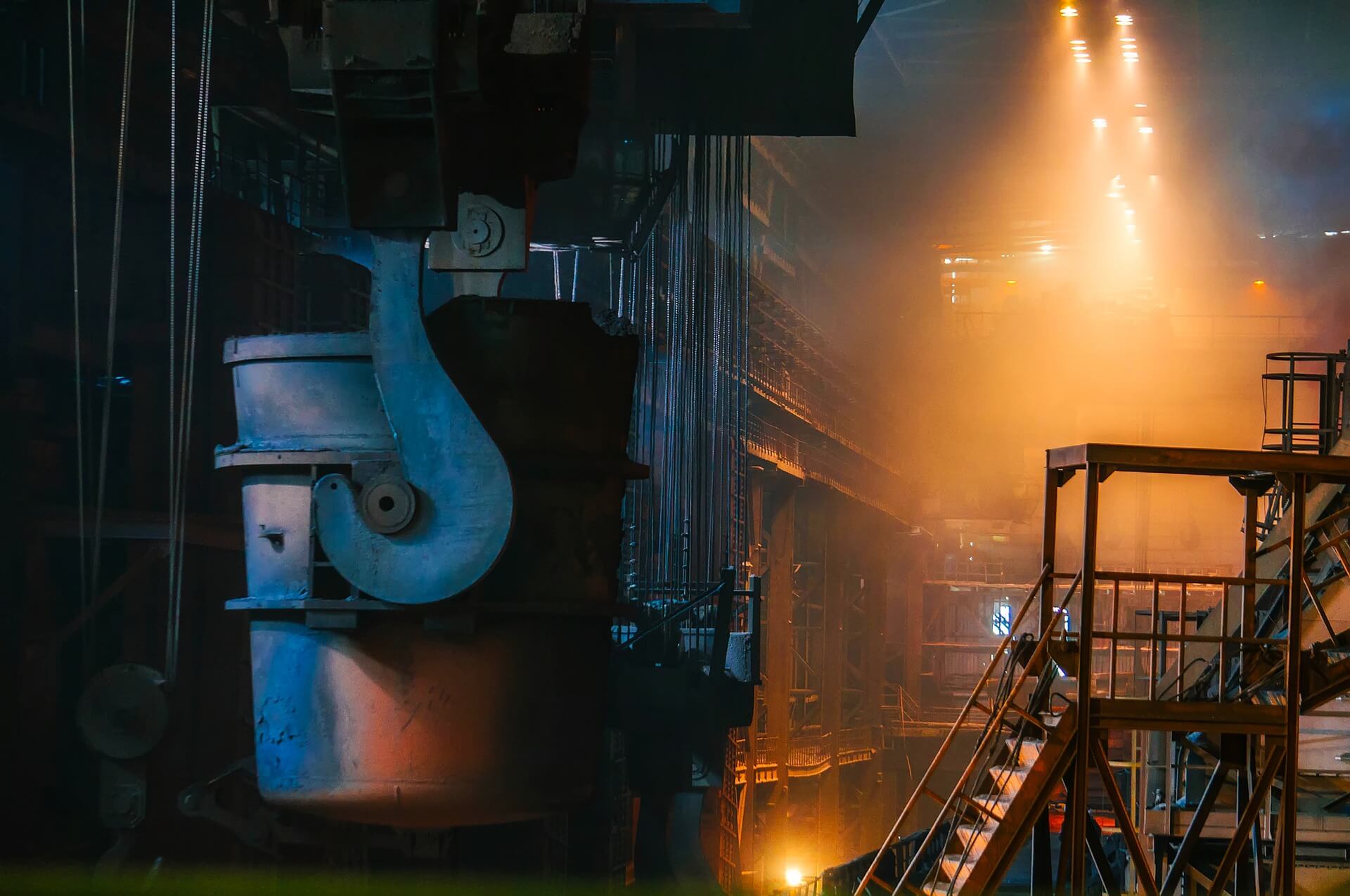
In manufacturing, energy costs are often exorbitant. In fact, they’re likely one of the biggest expenses for companies in the industry. To keep production on schedul—and equipment operational—you need to consider proper heating and cooling, lighting, operating power and much more.
While other industries discuss the idea of energy-efficiency and becoming green, it seems promising but highly unlikely for major manufacturers. It just takes a lot of power to run the factories, plants, and hardware necessary to produce things.
However, becoming more energy efficient and scaling back expenses would mean improving the bottom line. There would be fewer expenditures and money going out, yet the same if not more coming in. It’s a smart move, albeit one that may not seem as obvious to most manufacturing teams.
Believe it or not, there are some ways to decrease energy costs.
Going green as a team
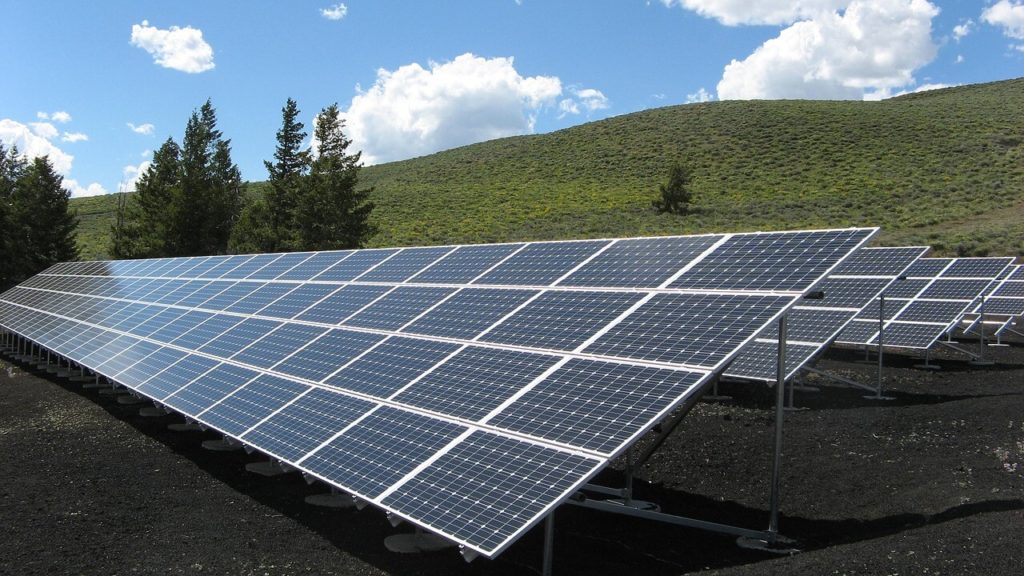
The shift towards energy efficiency does not end with the installation of new equipment like solar panels (pictured), but one must have a team committed to help in saving up energy. (Source)
Going green or becoming more energy-efficient is about more than just installing some new hardware and equipment and improving various processes. It requires a proactive team, ready to do what they can when they can to help conserve energy, including your employees.
That means educating your employees on the new energy-efficient policies and systems you are putting in place. Invite them to come up with some ideas for improving your consumption, and do what you can to listen and put weight behind their suggestions. Chances are, your workers understand what’s being done and what’s necessary. They know full well when something is wasteful, and when something can stand to be trimmed or optimized.
Get everyone involved and go green as a team.
IIoT and predictive analysis are on the rise
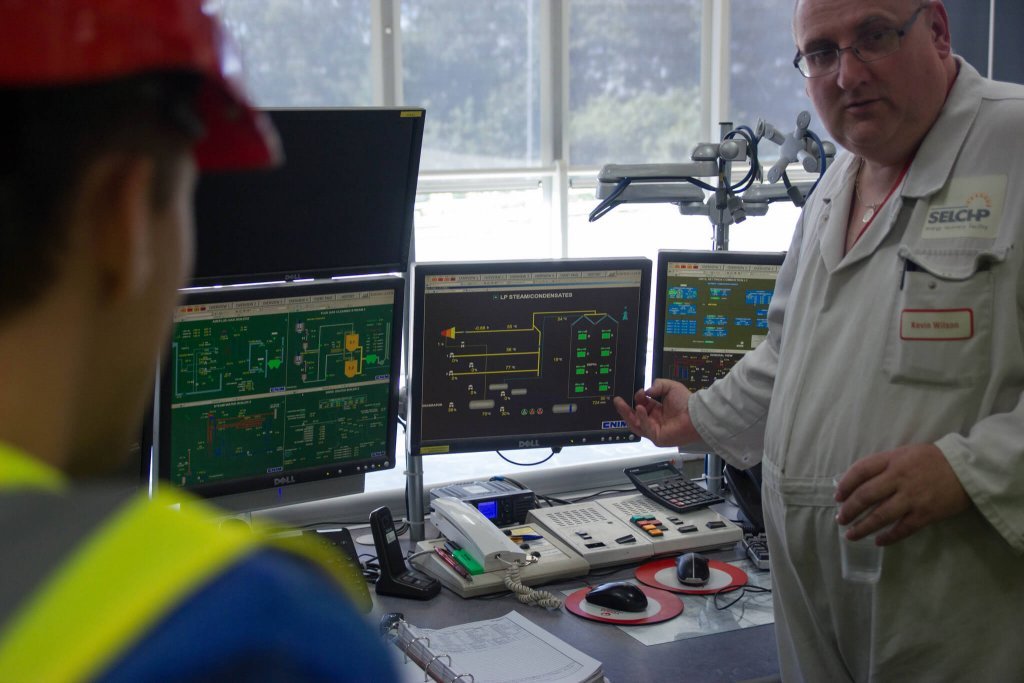
The Industrial Internet of Things is making its way into the manufacturing industry, and it can help in reducing energy costs. (Photo by Alexander Baxevanis via Flickr. CC BY 2.0)
According to Happiest Minds, IIoT, or the Industrial Internet of Things, is becoming hugely popular for many reasons. As a business strategy, it connects all the various pieces of the puzzle—every process and member of the manufacturing team—and helps ensure everything is in sync. The information and operational department can have a much closer, much more relatable relationship. This allows higher-ups to make better decisions that don’t work against their team, and it also helps improve overall efficiency. In many cases, it can even boost productivity.
By nature, it also opens up many opportunities on the predictive and proactive side of things. For instance, it can allow you to closely monitor equipment, no matter where you are, and take action as soon as you notice something isn’t quite right. It crowdsources the maintenance and monitoring of existing equipment, allowing you to retrofit old gear before it breaks down or runs into complications.
Energy retrofitting is another possibility that becomes available with modern IIoT systems.
Analyze your compressed air systems regularly
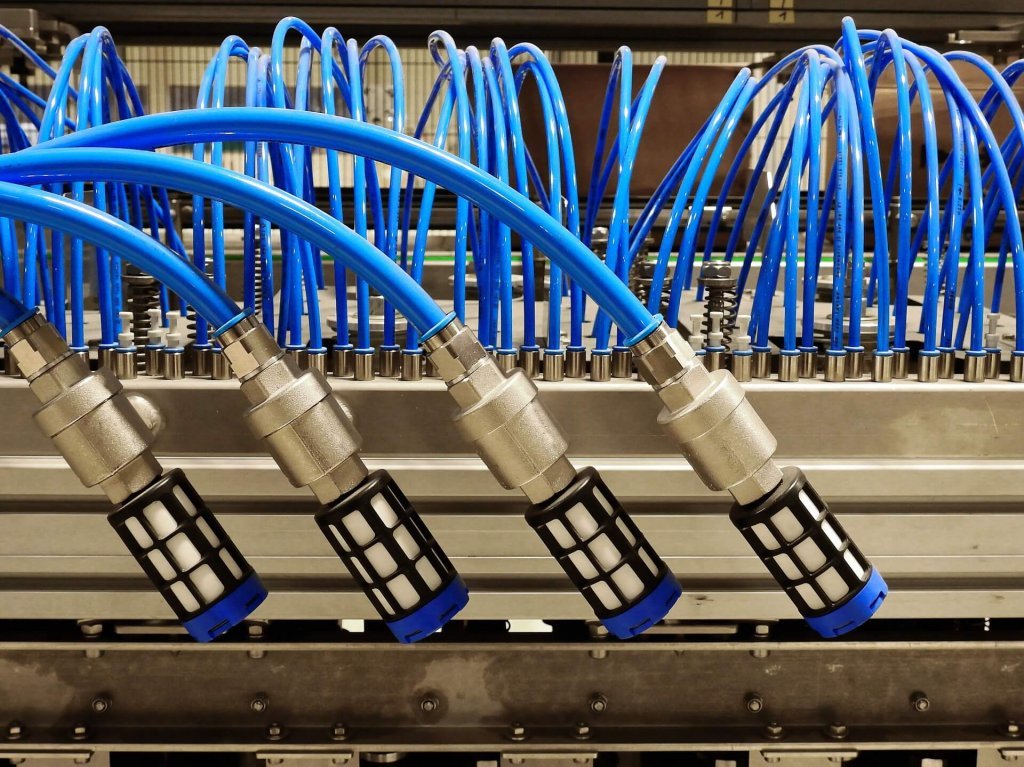
Energy expenses can rise because of leaks in compressed air equipment (pictured). (Source)
You may not realize it, but leaks in your compressed air equipment can contribute to a lot of wasted energy. This is more unfortunate when you consider the problem is easily remedied, albeit one many manufacturers overlook. Most of the time, fixing the problem involves tightening a fitting or seal or replacing a few parts.
In the United States, inefficient compressed air systems alone waste $3.2 billion each year.
Leaks also decrease a compressor’s output, making the equipment less efficient, and diminishing its reliability over time.
Be sure to audit your equipment and systems regularly, performing surveys to find leaks. You can also utilize ultrasonic detection equipment to find smaller, nearly invisible breaches too.
Install energy efficient lighting
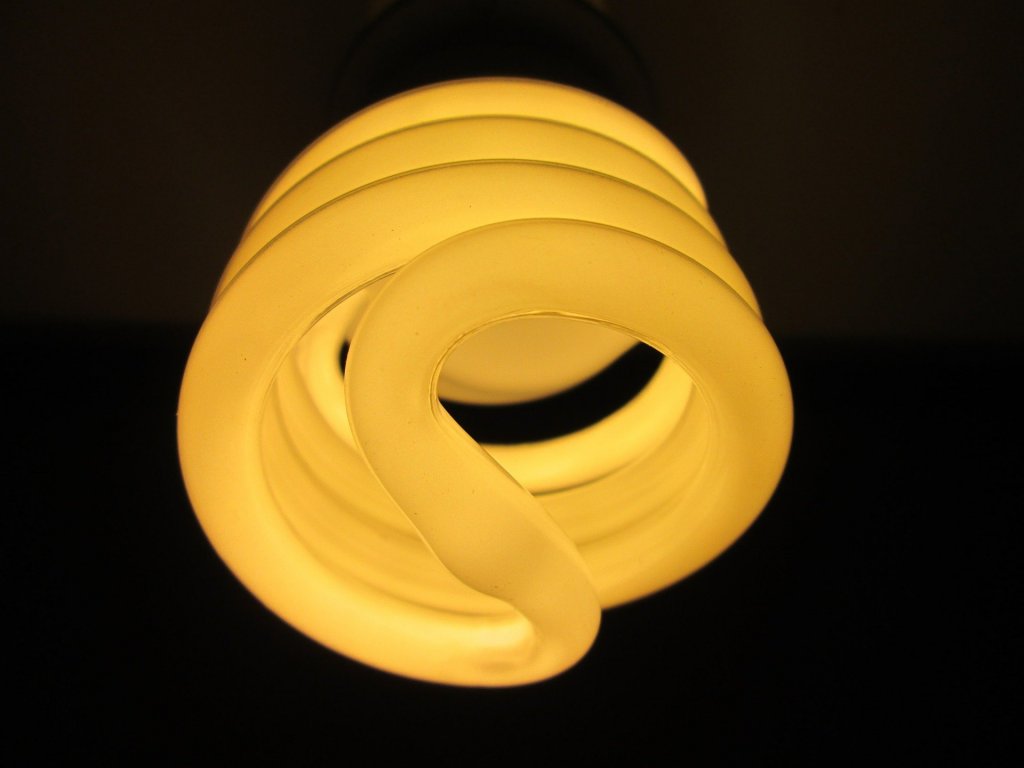
Use fluorescent light bulbs (pictured) to lower energy costs. (Source)
There’s no avoiding it — manufacturing facilities need to be well-lit, and the light sources used need to provide ample light. This can be bolstered even more by the fact that most plants and warehouses are large, closed-spaces where natural light doesn’t spread openly.
The trick is to replace conventional lighting with more energy-efficient technologies. Industrial compact fluorescent bulbs, called CFLs, and light-emitting diodes, or LEDs, are excellent replacement technologies. They use less energy and last much longer than conventional lighting.
You could also use automated systems — similar to smart home technology — to turn off and disable lighting in non-essential areas. For example, if no one is in the room and no movement is detected for a certain period, the lights can be turned off to conserve energy. Automated equipment and hardware don’t need light to operate, just human workers. When someone enters the room again, the motion detection system would turn the lights back on. Imagine the amount of money you could save just by turning off the lights in even a couple rooms or areas?
Improve process heating station
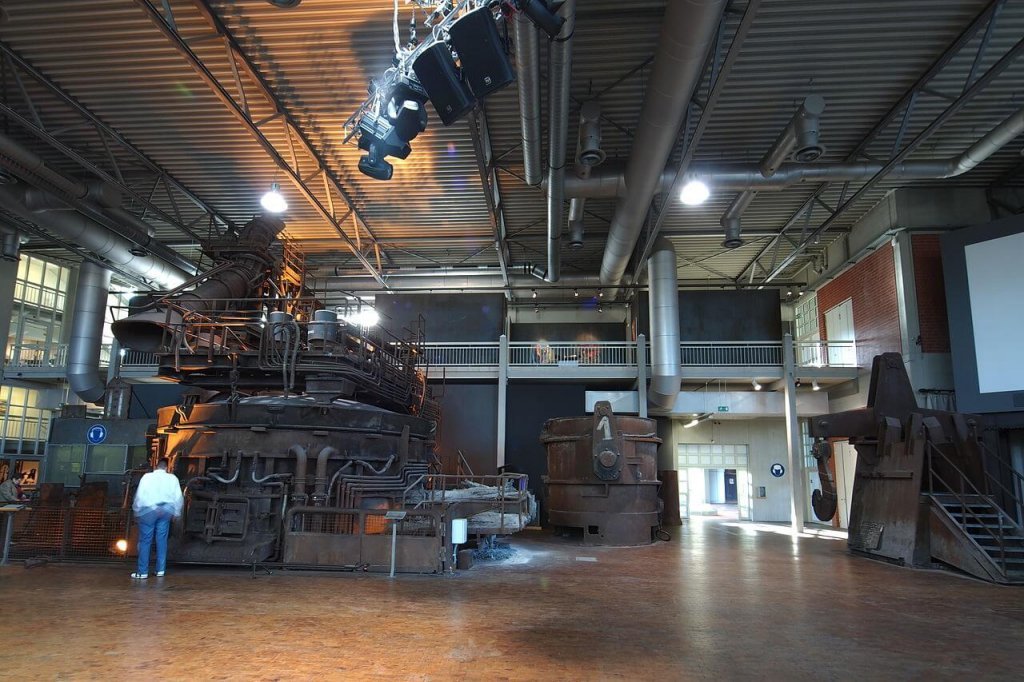
Equipping the plant or factory with new furnaces can also enhance energy efficiency. (Photo by Arnoldius via Wikimedia Commons. CC BY-SA 3.0)
When working with consumer and industrial goods, process heating is necessary. It can also be attributed to another major power eater for a location’s total energy consumption. If you’re not up to date with modern trends and technologies, you’d be forgiven for thinking this is an area of manufacturing that has not improved much.
There are tools and systems that will improve efficiency during process heating, like a heat recovery system, automatic blowdown controls, alternative fuels for more efficient combustion, and even new furnace installation and maintenance to lesson exhaust gases.
All these things can be leveraged to improve the process heating area of a facility and make it more efficient and lean.
Plan your consumption accordingly
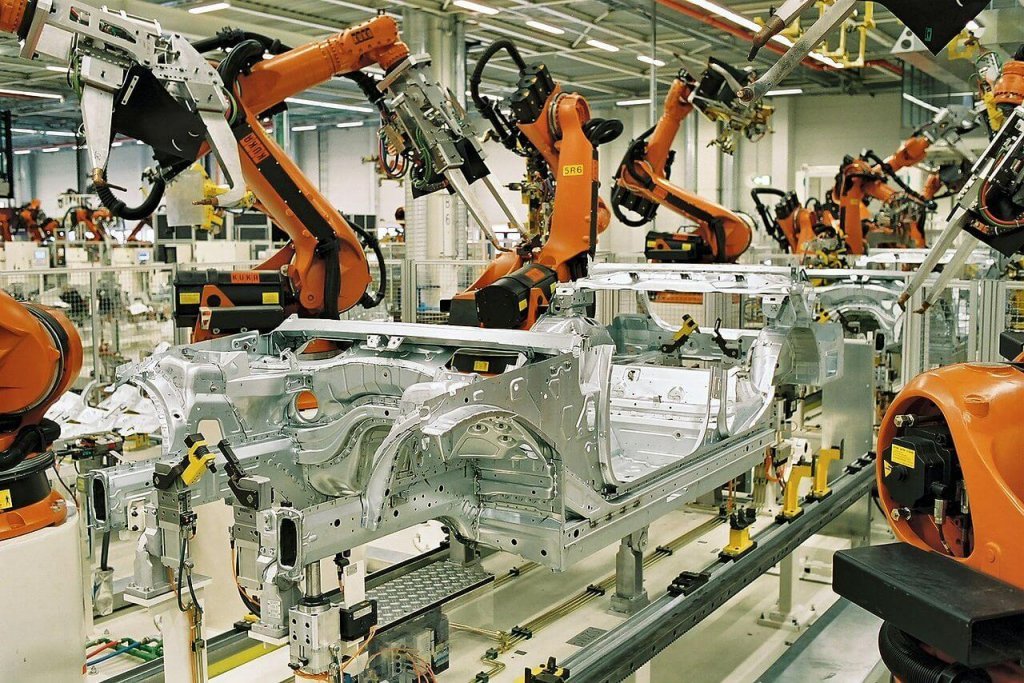
Using automated systems during off-peak hours can lower energy consumption. (Photo by BMW Werk Leipzig via Wikimedia Commons. CC BY-SA 2.0 DE)
Power and energy companies tend to create separate periods based on the amount of consumption being used. During peak hours, when people and businesses use the most power, they charge more money for the energy consumed. During low-production hours, or off-peak time, they charge less, because fewer people use power.
You can use this to your advantage and coordinate between peak production and peak consumption times. For example, running your heated hardware and automated systems at night when most people are sleeping can help you conserve costs. It also has the added benefit of reducing heat production, because it’s usually cooler at night. Plus, the requirements for additional power are decreased as your workers are likely home too, so less lighting is needed.
Origin Energy recommends tools like smart meters, IIoT monitors, and advanced hardware to ensure the power isn’t supplied until off-peak times.
Decreasing costs should be the goal of every business, but especially for energy-intensive manufacturing companies. Cutting these costs can have a direct impact on your bottom line, and that’s something worth striving for.
—
DISCLAIMER: This article expresses my own ideas and opinions. Any information I have shared are from sources that I believe to be reliable and accurate. I did not receive any financial compensation in writing this post, nor do I own any shares in any company I’ve mentioned. I encourage any reader to do their own diligent research first before making any investment decisions.

-
Crypto6 days ago
Bitcoin Slips, Ethereum Holds: Mixed Signals in Early Week Crypto Markets
-
Cannabis4 days ago
Germany’s Cannabis Legalization Backfires as Smuggling Surges
-
Crypto2 weeks ago
The Cryptocurrency Big Bang
-
Business6 days ago
Groupon 2.0? Giftify’s Q2 Trajectory Hints at Explosive Rerating
You must be logged in to post a comment Login