Business
Seven Things That Determine a Collaborative Robot Arm’s Flexibility
If you are in an industry that needs you to move fast and adapt to new market conditions, optimizing your facility for flexibility and versatility is essential to your survival and success. A good place to start is with the robots in your facility. Depending on large and fixed traditional robotic systems will do you no favor. Instead, what you should do is invest in good collaborative robots.
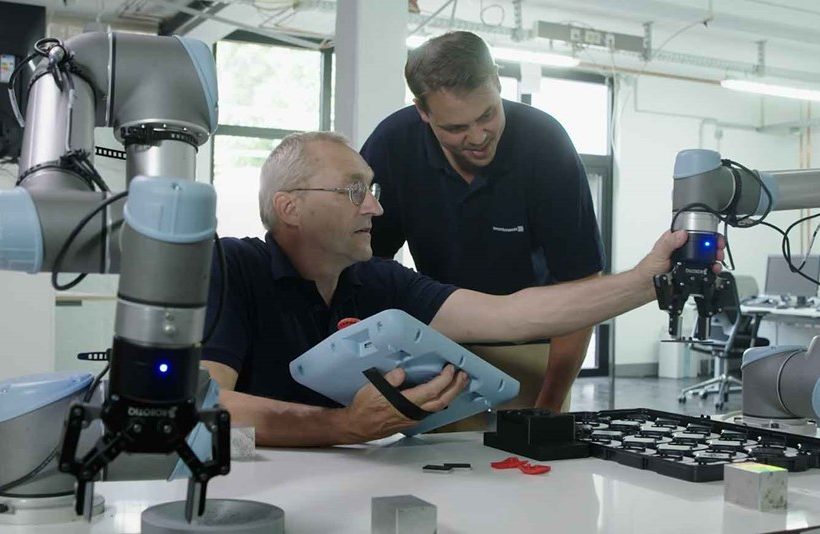
In the modern manufacturing environment, companies that learn to adapt to change are the ones that survive. Those that don’t, struggle and eventually die.
One of the things that play a role in determining a company’s adaptability is the ability to change its production processes. And the main determining factors of this are the cost of implementing such a change, and the time period that the given company can actually get things up and moving.
Collaborative robots give manufacturers agility that they didn’t get to enjoy with traditional robotic systems. However, not all collaborative robots are equally adaptable. Some are more adaptable than others. And one of the things that play a significant role in determining how flexible and versatile a given robot can be, is the robot arm that it is fitted with.
Here are things that you should pay attention to when choosing a robot arm since it will determine how limited your robot will be.
Size
Arms that take up relatively less space tend to give manufacturers more flexibility. This is because they can fit in very tight spaces, and so attaching them to any given spot in the production line is easier as you don’t have to worry about space. Therefore, the smaller the arm, the more freedom that an owner has to deploy the given robot to whichever section they deem needs the help.
Reach
A long arm allows a robot to do a wider variety of tasks. This is so especially with regards to tasks that need things to be moved from one place to the other.
There are also cases where certain tasks require a longer area of motion, and so a smaller arm will be useless. In such a case, the robot’s arm will limit the deployability of the robot, even if the robot is capable of executing the task in question.
Therefore, the longer the reach of the arm that you choose, the more freedom that you will have. Generally, an arm with a longer reach gives a person more options in terms of which activities a robot can be assigned to do.
Ability to be reprogrammed
In the current environment, it is normal for a small company to have to pivot from one strategy to the other. Manufacturing processes may change with the emergence of new technologies. And there may be a need to shift into a different sector altogether — in order to explore or take advantage of emerging opportunities.
In order for an arm to effectively handle the different tasks that such changes come with, it will need to be reprogrammed. Some arms are limited as far as programmability is concerned. Others, while they can be reprogrammed, need specialized expertise. Generally, if you want to maximize flexibility, you need to look for an arm that is easily reprogrammable.
Compatibility with end-effectors
End effectors determine what a robot arm can do. It is what determines what the robot can pick or move, how it does it, and the type of tools that it can use.
There are a lot of different end effectors in the market, and each manufacturer usually has its own specifications. They are also capable of doing different tasks. Therefore, they play a significant role in determining which tasks a robot can execute.
Some arms come already customized for certain end effectors. These are not ideal for use in an industry that prioritizes adaptability. Arms that can easily accommodate different types of end effectors are thus ideal for a company in such an industry since they allow for more flexibility.
Payload capacity
In the course of changing tasks, a robot arm will have to handle different weights. Therefore, the main thing that one should consider here is the size and weight of the products that their organization produces. If there are tasks that may require the robot to lift and operate tools, then the weight of these tools should also be considered.
Generally, the higher the maximum payload capacity of an arm, the more versatile the arm will be. This is because it means that the arm can handle a wider variety of weights. And so if you want to future-proof your company, opting for a robotic arm that has a high maximum load capacity is a good place to start as it will give you more freedom as far as deployment is concerned.
Weight
Lightweight arms are easier to move. This makes for an easier installation process. Deploying them from one section to the other is also easier. Therefore, they offer a degree of convenience that makes them incredibly user-friendly and easy to use in different scenarios — something that makes the process of transitioning smoother.
In cases where a facility has limited space, a lightweight arm, and a lightweight robot can be really convenient. This is because heavy robots and robotic arms are harder to fit on shelves. They will need a more stable surface. And they may also need to be shielded away simply because of exaggerated consequences of the arm falling on someone or property.
Therefore, a lightweight robot arm will give you more freedom in terms of where you can place and install it. You also don’t have to worry about taking as many safety precautions as you would have had to have you been dealing with a heavier robot arm.
Ability to reuse programs
An arm that can easily reuse programs is easier to redeploy. This is because, with such an arm, you don’t have to completely reprogram the arm or use completely different software every time there is a change of tasks. This will reduce redeployment time. It will also help to make the process less stressful. Such an arm is thus inherently more flexible than one which has a limited ability to re-use programs.
If you are in an industry that needs you to move fast and adapt to new market conditions, optimizing your facility for flexibility and versatility is essential to your survival and success. A good place to start is with the robots in your facility.
Depending on large and fixed traditional robotic systems will do you no favor. Instead, what you should do is invest in good collaborative robots. Their size, ability to be deployed in less than a day, versatility, and enhanced safety features, make them ideal for the current manufacturing environment.
__
(Image courtesy of UNIVERSAL ROBOTS)
DISCLAIMER: This article was written by a third-party contributor and does not reflect the opinion of Born2Invest, its management, staff, or its associates. Please review our disclaimer for more information.
This article may include forward-looking statements. These forward-looking statements generally are identified by the words “believe,” “project,” “estimate,” “become,” “plan,” “will,” and similar expressions. These forward-looking statements involve known and unknown risks as well as uncertainties, including those discussed in the following cautionary statements and elsewhere in this article and on this site. Although the Company may believe that its expectations are based on reasonable assumptions, the actual results that the Company may achieve may differ materially from any forward-looking statements, which reflect the opinions of the management of the Company only as of the date hereof. Additionally, please make sure to read these important disclosures.

-
Markets4 days ago
Stock Markets Surge Amid Global Uncertainty, But Storm Clouds Loom
-
Cannabis2 weeks ago
Aurora Cannabis Beats Expectations but Faces Short-Term Challenges
-
Africa13 hours ago
Morocco Charts a Citizen-Centered Path for Ethical and Inclusive AI
-
Crowdfunding1 week ago
Savwa Wins Global Design Awards and Launches Water-Saving Carafe on Kickstarter