Business
How lean manufacturing leads to a competitive advantage
The implementation of lean manufacturing in your company can help boost your business while reducing waste in the process.
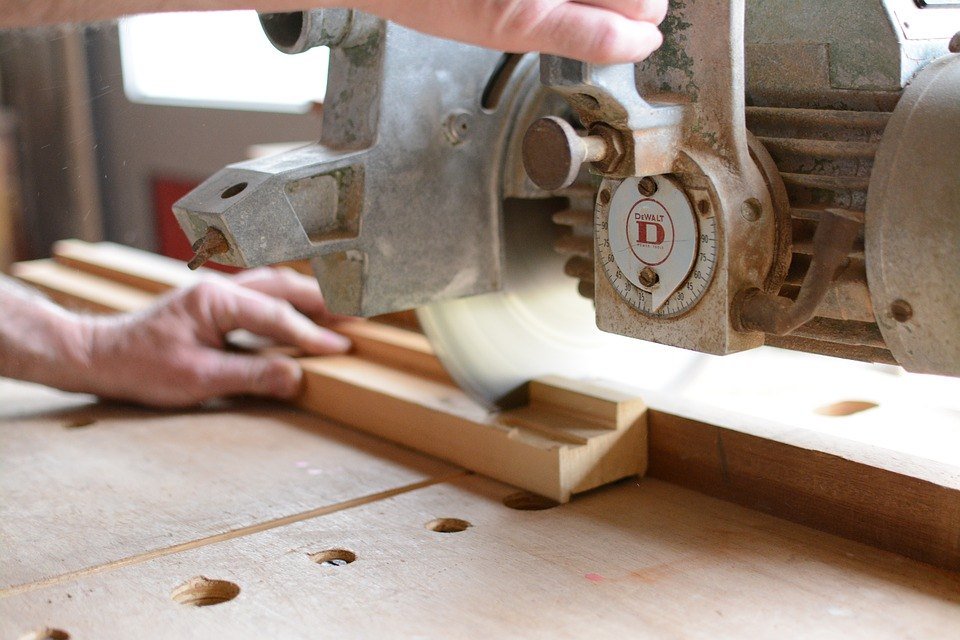
Lean manufacturing, often referred to as just “lean,” is a process manufacturers can adopt into their operation that helps to reduce as much waste as possible. The more tenants of lean manufacturing you follow, the greater the benefits you’ll experience. Discover how lean manufacturing gives you a competitive advantage in the marketplace in addition to the benefits you see in your facility:
1. Improves customer service
Customer service improves when you focus on decreasing waste at your facility. The key to lean manufacturing is to reduce the 95 percent of production time that does not add value to a product. Reducing this time gets the products to the customer faster. It also focuses more time on adding value to the product, which makes for satisfied customers — you’ll have an automatic advantage over companies that waste time and don’t cater to customer needs.
2. Makes employees happier
In addition to producing satisfied customers, lean manufacturing also makes your employees happier. When your employees are content, you’ll need to hire fewer new workers because your existing workers will want to stay.
It’s not just a theory that employees have a better work environment at a lean manufacturing facility. A study of lean manufacturing employees from the European Journal of Logistics Purchasing and Supply Chain Management indicated employees reported lower staff turnovers, better cross-section competence and reduced stress levels.
3. Lowers costs
The basic approach of lean manufacturing is to reduce wasted time in processing. By cutting waste, you’ll reduce excesses in your shop and lower costs, and both inventory and operating costs drop through lean manufacturing.
The seven areas of waste — inventory, over-processing, transport, waiting, motion, defects and overproduction — contribute to higher production costs. Lessening the waste in these areas will cut your costs and allow you to focus on adding to product value. Doing so means making better products for less money, which raises your profits.
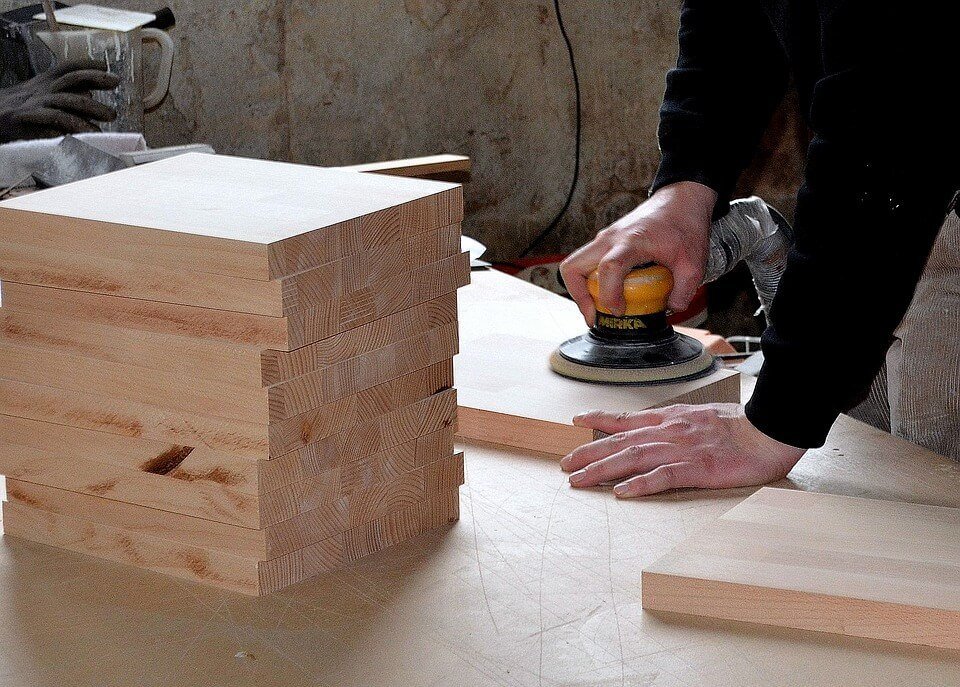
The pull production process in lean manufacturing reduces lead time since the product is shipped whenever it’s ready, instead of waiting for a whole batch of products to be finished. (Source)
4. Reduces lead time
When you implement lean manufacturing, you’ll be implementing pull production rather than batch production. That means each product moves through the system when it’s ready instead of waiting for the entire batch. Pull production is much more efficient than producing by the batch, and lead times drop with this process. According to the European Journal of Logistics Purchasing and Supply Chain Management, if you change from traditional batch production to pull production, you could see a 90 percent drop in lead time.
5. Increases product quality
The entire reason for lean manufacturing is to focus on improving product quality through reducing waste. You spend more time on product production and less on needless activities or waiting. Automatically, your product quality will increase, and better products will make you more competitive in the marketplace. Additionally, since you can produce better products for less money, you can sell them at a lower price. This gives you an edge over your competitors who may charge more for similar products that are not as high of quality.
Incorporating lean manufacturing in your plant
If you want to gain this advantage, you need to remove the seven areas of waste from your production. Switch from batch processing to pull processing to cut lead times. Additionally, you’ll want to assess your inventory and remove unneeded parts and products. Only produce what is needed immediately to avoid overproduction. And consider changing shipping so you send more products with each shipment. This lowers transportation costs.
Allow employees to help with problem-solving on the floor. This gives them autonomy in their work, making them happier. When workers contribute their ideas for saving time and overcoming problems, you can solve the issues without spending too much time and money. Lean manufacturing techniques such as these can make it easier to do more in your facility for less.
Competition and lean manufacturing
Incorporating lean manufacturing techniques into your facility may require a shift in your thinking from traditional manufacturing — but this process sets you apart from your competitors. No matter what step you are in the production process, you can benefit from lean manufacturing and boost both sales and profits.
—
DISCLAIMER: This article expresses my own ideas and opinions. Any information I have shared are from sources that I believe to be reliable and accurate. I did not receive any financial compensation in writing this post, nor do I own any shares in any company I’ve mentioned. I encourage any reader to do their own diligent research first before making any investment decisions.

-
Crypto2 weeks ago
PayPal Continues to Bet on Cryptocurrency
-
Markets4 days ago
Commodity Futures Snapshot: Wheat Softens, Corn Pressured, Soybeans Steady
-
Markets2 weeks ago
Commodity Futures Markets Struggle Under Weight of Strong Harvests and Global Uncertainty
-
Crypto4 days ago
Stripe and Paradigm Reportedly Working on a New Blockchain Called Tempo
You must be logged in to post a comment Login