Business
Why manufacturers lost so much money in 2016
Bad training is no one’s goal, and yet plenty of manufacturers either turn a blind eye to training inconsistencies or remain stuck in the past despite availability of better options for effective training.
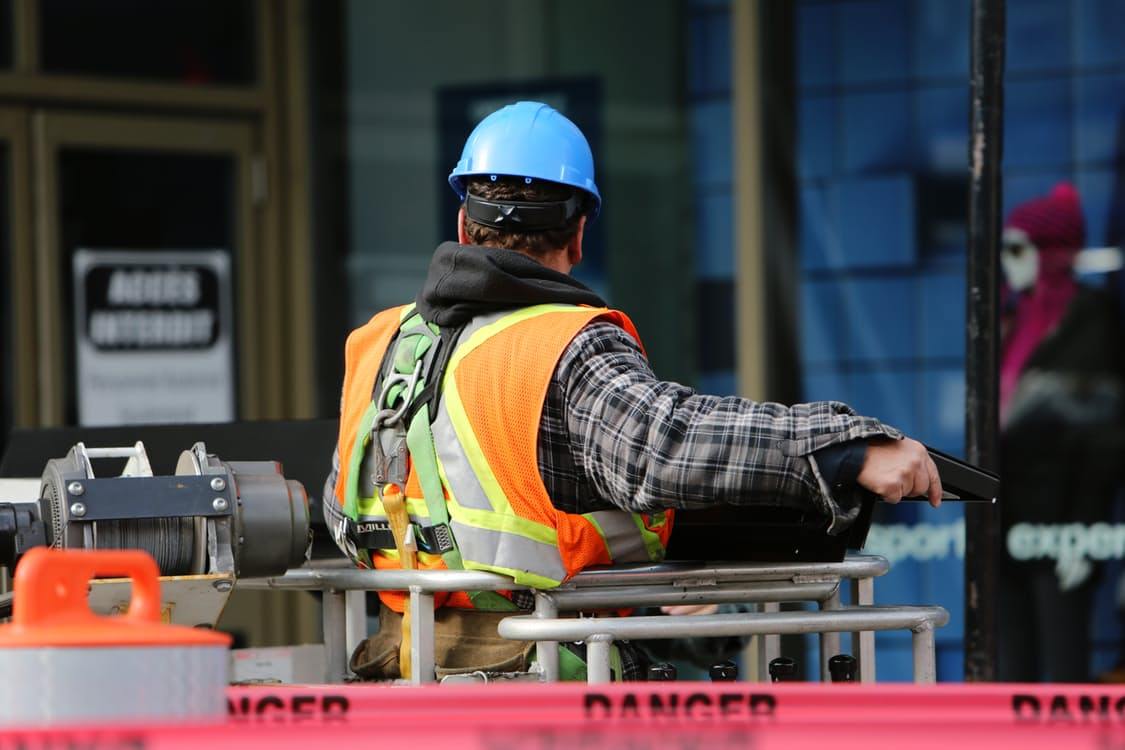
There are many ways to lose money over the course of a year, mostly to circumstances beyond your control. But there are two ways manufacturers lost money this past year that were entirely preventable: improperly trained employees and equipment damage.Here’s why.
The cost of bad training to your organization
Bad training is no one’s goal, and yet plenty of manufacturers either turn a blind eye to training inconsistencies or remain stuck in the past despite availability of better options for effective training. Is it complacency? A belief that their training is “good enough?” Concern about the cost of making changes?
It’s a little of each of those things – with an emphasis on the third point. But the reality is inadequate training costs far more than anything you could spend on updating your methodology.
Let’s start with your workforce. How they perform directly impacts your bottom line – and how they are trained directly impacts how they perform! Says Oak Tree IT, “Untrained employees lack the skills and knowledge to produce high-quality products and results.”If you’re not putting out a quality product, you won’t be in business for very long.
There’s an argument for better training right there. Productivity is another one.
A study of more than 3,100 U.S. workplaces by the National Center on the Educational Quality of the Workforce (EQW) found “a 10 percent increase in workforce education level led to an 8.6 percent gain in total productivity. But a 10 percent increase in the value of equipment increased productivity just 3.4 percent.”
The type of training you offer also affects your turnover rate – something 70% of organizations agree has a negative financial impact, reports SHIFT eLearning. And unfulfilled employees don’t tend to stick around.
Putting it into numbers, CDL claims the average cost of replacing employees is 16% of the annual salary for positions earning $30,000 annually or less, 20% for positions earning $30,000 – $50,000, and up to 213% for “highly trained employees holding executive positions in the organization.”
Finally, bad training can result in serious mistakes on the job – the kind that result in injury, or even loss of life. That alone should be incentive enough to ensure your training is everything it needs to be – but because these kinds of incidents seem rare, they often aren’t considered part of the equation.
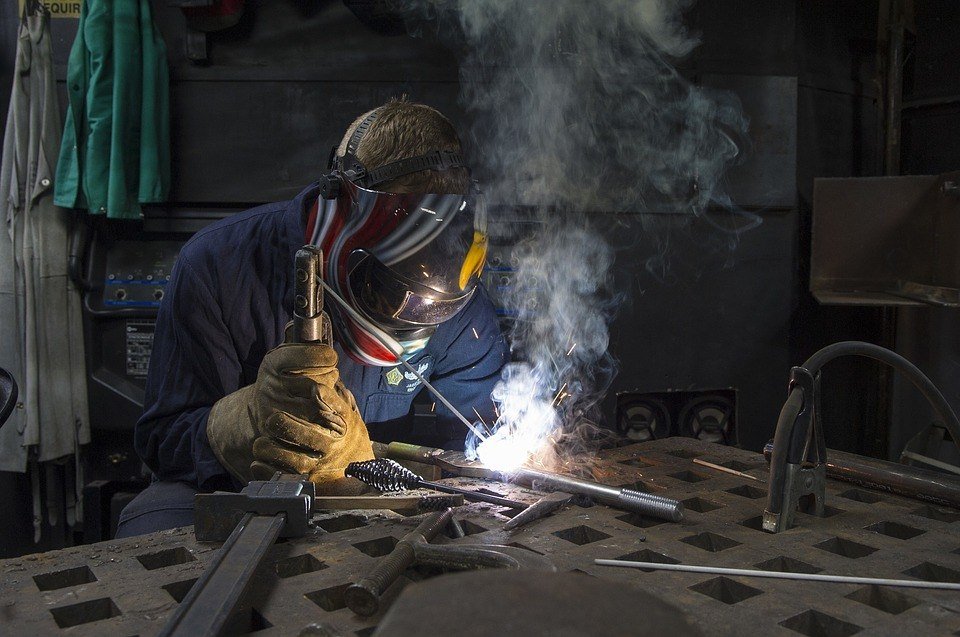
Inadequate training costs far more than anything you could spend on updating your methodology. (Source)
The cost of equipment damage
And what of item two on our list of avoidable costs? The ramifications of equipment damage are just as involved as those resulting from bad training – and more often than not incur costs beyond the equipment itself.
Even small-scale damage can cost your organization quite a bit: “The breakdown of any one part can bring the entire operation to a halt until the problem is identified, a solution found, and repairs or changes made. The problems may arise from a number of sources.”
But sometimes equipment damage is the cherry on top of a larger issue. For an extreme example, let’s look at the case study of last February’s crane accident in New York City, where a number of factors resulted in equipment damage – and then some.
Here’s a breakdown of the fallout from this single, seconds-long incident:
- 3 injuries
- 1 death
- Immediate and prolonged work stoppage while the incident was investigated
- Workers’ compensation costs
- Resultant water and gas line repairs on the street where the incident occurred
- Removal of the collapsed crane
- Removal of parked cars crushed by the crane
- $30 million lawsuit filed by one injured victim
- A minimum fine of $4,800 for not safeguarding use of the equipment
- PR expenses for all involved as they try to rebuild their reputations
And this list doesn’t even factor in the cost of the destroyed crane itself!
Whether damaged equipment results in an accident or the other way around, it’s not worth the risk.
How these two costs are connected
If this all sounds like apples and oranges, it isn’t. Here’s where these two costs intersect – bad training often causes the misuse that damages equipment!
So there’s a greater argument to be made for investing in better training for your workforce. You can’t avoid the wear and tear – and associated maintenance and repair costs – of regular equipment use. But you certainly can avoid the heightened wear and tear that comes from overuse and misuse of equipment as a result of poor training.
How? By modernizing your approach – incorporating technology like 3D interactive simulation, and even virtual and artificial reality components.
For starters, these modalities save time, and time, of course, is money.
“One of biggest benefits we’ve experienced is being able to use it in multiple areas for both logistical training and for sustainment needs,” says the Product Support Training Manager at Oshkosh Corporation. “Annual refresher trainings are very costly when one has a large user base. For example, virtual stations can accommodate 20-30 students in class, letting them operate a truck virtually, experiencing the driver interface in a way that would’ve taken us infinitely longer if they had to do it one at a time.”
Moreover, making this change allows for the difference between struggling to respond, and knowing exactly how to respond in any situation.
Returning to the NYC crane collapse example, Equipment World noted:
“We can only speculate that if the crane operator had better communication then maybe the boom could have been lowered sooner. Or maybe someone on the ground crew could have told him to keep the boom angle above 75 degrees. Those kind of precise, emergency maneuvers are more likely to be successful if uninterrupted, real-time communication is in place.”
Or if the situation is so practiced it becomes second nature – as familiar as any other routine task. This is where simulation training becomes invaluable – offering an opportunity to safely and regularly perform infrequent, dangerous tasks until they are ingrained and part of workers’ muscle memory.
Not only that, digital devices like the iPad have inspired an evolution toward training that is scalable, modular and portable. This kind of accessibility makes upgrading your training super affordable, while allowing for easy ongoing and refresher training.
Adding modern technology to your training program doesn’t have to replace what’s already working well – it simply complements it. It also lets your workforce know you care enough to provide top-notch training – something that’s attractive to new hires in up-and-coming generations like Millennials as well.
So don’t fret about the cost of updating your training – not doing it is already costing you more than enough. Make this one change, and 2017 will be your most prosperous year yet.
—
DISCLAIMER: This article expresses my own ideas and opinions. Any information I have shared are from sources that I believe to be reliable and accurate. I did not receive any financial compensation in writing this post, nor do I own any shares in any company I’ve mentioned. I encourage any reader to do their own diligent research first before making any investment decisions.

-
Markets3 days ago
Stock Markets Surge Amid Global Uncertainty, But Storm Clouds Loom
-
Cannabis2 weeks ago
Aurora Cannabis Beats Expectations but Faces Short-Term Challenges
-
Crowdfunding1 week ago
Savwa Wins Global Design Awards and Launches Water-Saving Carafe on Kickstarter
-
Biotech2 weeks ago
Asebio 2024: Driving Biotechnology as a Pillar of Spain and Europe’s Strategic Future
You must be logged in to post a comment Login