Business
How technology is disrupting the metal fabrication industry
Technology is helping how industries carry out their processes. Here are the trends that are making a change in the metal fabrication industry.

For years, the metal fabrication industry has slowly been evolving to keep up with modern trends and technologies. This is despite a long history of stagnancy in this regard, with a wide variety of legacy systems, tools and strategies slowly becoming obsolete.
One of the biggest drivers for this change is, of course, not just modern technology as a whole, but smarter, more efficient systems thanks to a “connected” world—more specifically, smart technologies that are now available via an open and constant internet connection. You wouldn’t think this has any bearing on a manufacturing market like metal fabrication, but it most certainly does.
According to Industry Week, IoT and connected machinery are altering the landscape so much that the modern factory or plant operates worlds different from those of yesterday. The same is happening in metal fabrication, in fact—what with the likes of 3D printing, laser cutting and fabrication methods, we’re seeing fewer demands for steel and multiple disruptive digital technologies.
To explore a little further, here are five of the most disruptive trends or technologies taking hold in the metal fabrication industry today.
1. 3D printing
During the early days, 3D printing was very much a product development and conventional manufacturing tool, outside of the consumer-level printers. But the technology has advanced to the point where it’s now viable in industrial settings. This is especially true of the materials used, which were commonly plastic and soft-based but now include things like steel, concrete and even masonry.
The printers themselves are much larger—and growing every day—to accommodate a variety of use cases, too. In China, for example, an entire building was created and assembled using 3D printing methods as mentioned in Arch Daily.
The nature of the technology is disruptive in fabrication because it alters how components are developed, ordered and maintained. However, it also affects overall waste—with 3D printing, there’s much less of it, which also means we can optimize energy usage. It’s greener in the sense that it’s more efficient, but that comes with a variety of benefits for product and component development as well, like much faster development cycles.
2. Lowered dependence on steel
Thanks to modern innovations—both concerning new development practices and technology advancements—there’s less need for steel across a variety of markets. Since steel is a relatively expensive material in bulk, as is working with it, this helps manage a range of financial burdens.
With more enhanced development practices, it’s needed in fewer quantities, which helps speed up developments and lower overall costs. Thanks to material sciences and the use of additive manufacturing, more materials can be used in place of steel, too. In some cases, said materials are just as strong if not stronger in their current implementations. This includes elements such as aluminum, cobalt derivatives, titanium and similar metals.
3. Disruptive digital channels
When discussions about disruptive digital technologies arise, the topic of choice is generally 3D printing, but that’s more obvious. Other digital channels are altering the landscape, as well, many of which have to do with the “connected” internet-enabled functionality of modern tech.
Big data systems, for example, can be used to enhance operational efficiencies and business strategies, alongside delivering more personalized customer experiences. This may not seem like it has any inherent connection to the metal fabrication industry, but it heavily influences the supply chain and product or component development. This could also lead to better or more personal customer relationships, cloud-based technologies and systems usage, as well as more varied online or digital experiences.
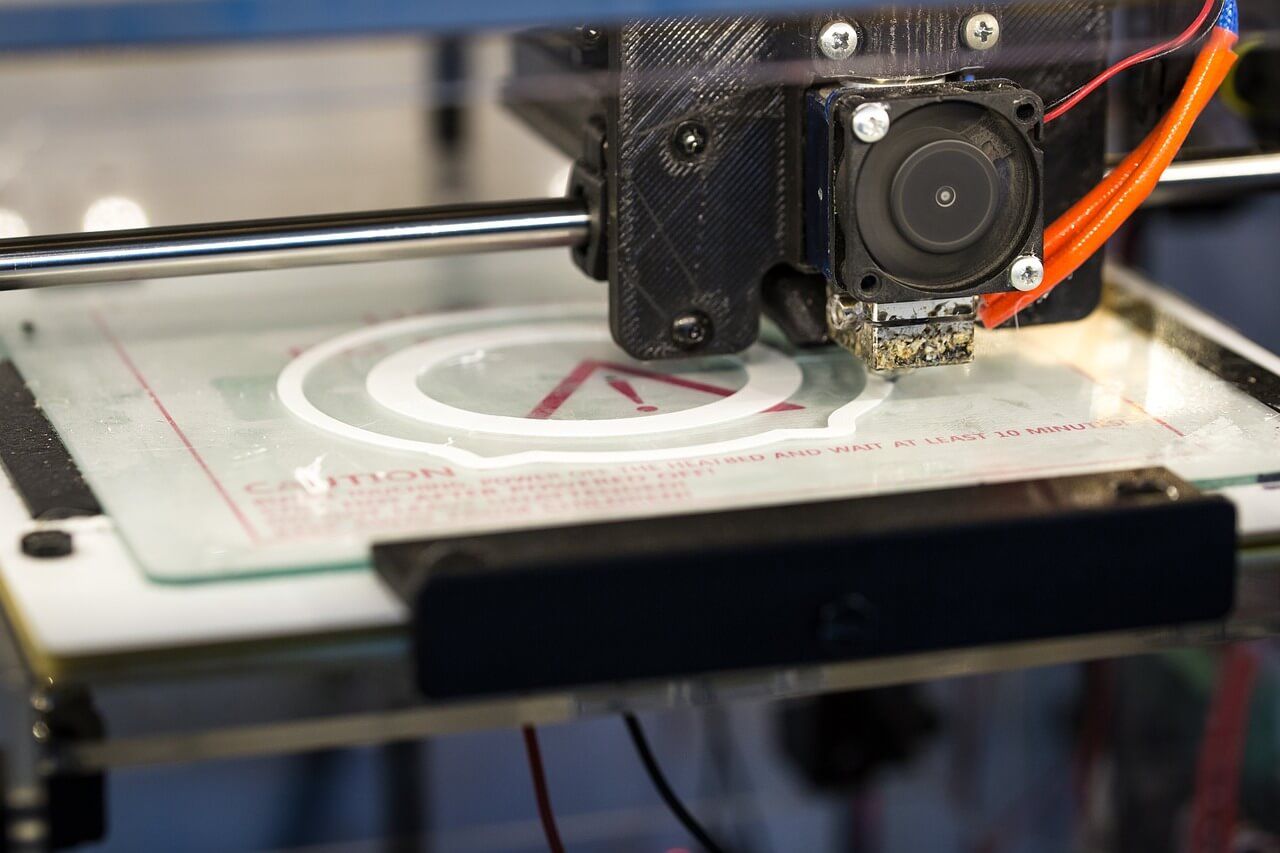
Technologies such as 3D printing do not just offer a more optimized use of energy, it also delivers faster product development cycles. (Source)
Consider, for instance, how new products and services are ordered today—online through remote technologies. Two partners—one being the client and the other being the metal fabricator—may never have any physical or direct interactions, only those facilitated via online systems. The client buys or orders a specific series of components, the fabricator follows specifications and develops them, completes a quality assurance process—all remote mind you—and then ships the finished goods or parts.
4. Cyclical or green economy practices
3D printing has brought to light the many ways in which the metal fabrication industry can improve its processes both for the environment and internal efficiency. We are seeing this happen in many other areas too, such as steelwork. Newer, more innovative goals are being adopted to share, reuse and re-manufacture with steel and similar metals, so as not to increase an already abundant amount of waste.
Many forms of precision sheet metal manufacturing, 3D or additive manufacturing, subtractive milling and grinding and similar types of development—and their subsequent technologies—are being used in the current industry.
Green advances can and will have a significant influence on current steel demands, as well as demand into the future. Specific projects, for example, are highly suitable and ideal for re-manufactured materials, whereas others are not. This may lead to a certain balance in the industry, which helps level demands for various materials, processes and goods.
5. Robots and automation
This may be much closer to the far horizon, at least regarding fully automated and autonomous implementation, but it’s still coming. The Fabricator notes that thanks to machine learning and AI, advanced robotics and automation systems are being adopted across manufacturing industries to supplement human workers. You can’t expect human employees to continue operations 24/7, as they need breaks or may suffer exhaustion and injuries from time to time.
Robots, on the other hand, can continue operations indefinitely, so long as they are maintained well, and the proper systems are in place. That’s exactly why we’re using and improving AI and machine learning technologies.
We may soon see the day where metal fabrication plants and factories are almost entirely comprised of advanced robotics and automation systems. Customers order their components, the information is sent digitally to the factory and the system prints the items. They are then reviewed, packaged and shipped with little to no external input—as accurately and reliably as ever to boot.
Dealing with the challenges
Some of the most significant challenges will arise from incorporating these new systems and technologies. Advanced robotics and automated systems, for instance, will take some time to perfect. It will be a lengthy process of development and review before we can trust the systems to operate with little oversight.
Green practices will evolve, as well, as we learn more about the materials in use and the technologies coming to fruition. The recycling and re-manufacture of materials have always been a thing, but it’s more prominent today. On top of that, the involved parties are always looking for new ways to improve the devices in use, which includes making them more efficient and environmentally friendly.
Whatever the case, these technologies are indeed changing the face of modern metal fabrication for the better. Expect to see an entirely different landscape soon, if not already.
—
DISCLAIMER: This article expresses my own ideas and opinions. Any information I have shared are from sources that I believe to be reliable and accurate. I did not receive any financial compensation in writing this post, nor do I own any shares in any company I’ve mentioned. I encourage any reader to do their own diligent research first before making any investment decisions.

-
Crypto6 days ago
XRP at Crossroads: Price Slips as Utility Questions Loom
-
Biotech3 days ago
AI Project Identifies New Biomarkers for Rare Sarcomas
-
Africa2 weeks ago
Kenyan Fintech HoneyCoin Bets on Stablecoins to Transform Africa’s Financial Infrastructure
-
Markets5 days ago
Corn Yields Questioned Despite Strong Exports and USDA Projections
You must be logged in to post a comment Login