Business
How construction companies are embracing environmental compliance
Construction companies should be able to adapt to the changing needs of our environment, which means updating and reforming outdated methods.
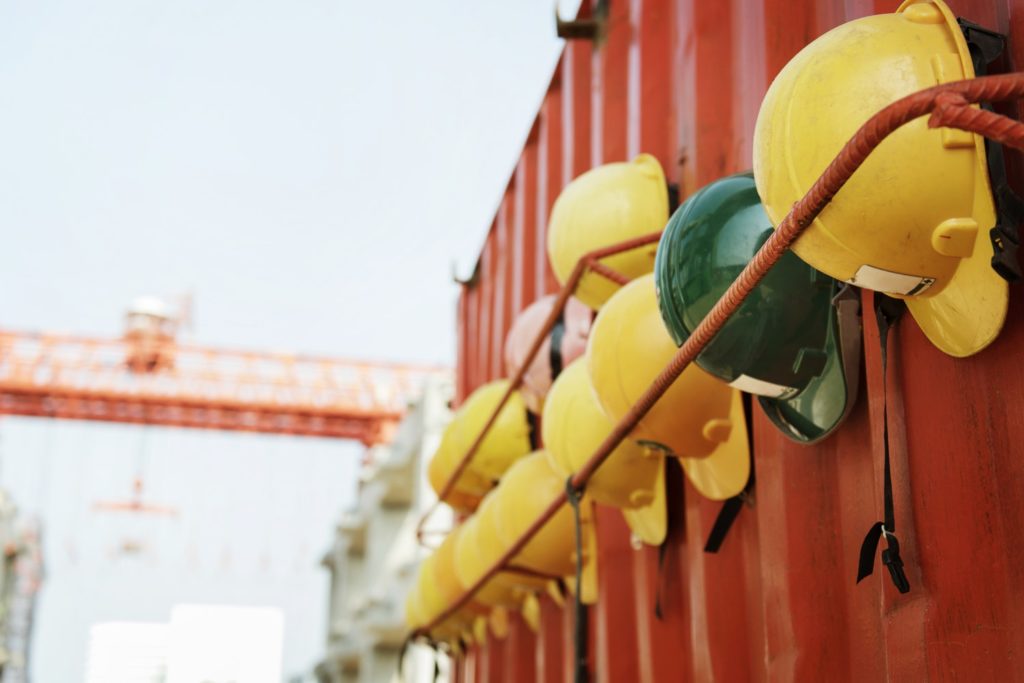
The preservation of the planet is a shared responsibility. Companies in every industry must make a collective effort to align with ecofriendly practices, striving to reduce carbon emissions and excessive waste with sustainability as the primary goal. Environmental compliance provides a foundation on which to build.
Construction companies deserve special attention in this regard, not for the emissions and waste inherent to their industry but for the impressive ways they’ve embraced change. Their adaptability in reforming old, outdated methods and restructuring obsolete models of management is essential to acknowledge.
In learning from the success of today’s construction companies, organizations in similar industries can assess and address their own flaws and weaknesses. As we explore programs, policies and technologies, managers might make a note of some of the modern strategies employed for environmental compliance.
Let’s examine the subject in greater detail, exploring how the construction industry has moved in a positive direction.
1. Environmental management systems
An environmental management system, otherwise known as an EMS, allows a construction company to set performance goals and enlist their workforce to achieve them. They’re essentially an organizational tool that simplifies operations, and they’re used when a manager needs to determine all applicable environmental requirements.
Among other relevant information, an EMS also informs the project manager when and where to file permit applications, instructs them on prevention plans and delegates the responsibility of different types of paperwork. And this list is only a fraction of what an environmental management system does for a crew.
The EMS also provides action plans with information on management best practices, instructions for installation, training materials and auditing checklists for emergency procedures and onsite compliance. When it comes to the benefits of an EMS, reductions to emissions and waste are just the beginning.
The thorough, exhaustive nature of an EMS can also identify hidden opportunities to save money through more efficient processes. When they’re reviewing the basics of these systems, managers should also note their potential for team building, improved morale and a better reputation among clients and communities.
2. Choosing to rent modern equipment
Heavy equipment is expensive to purchase, and year after year, suppliers release upgraded machinery with new technology. Choosing to perpetually purchase and replace existing equipment is both unsustainable and unrealistic. That said, compliance with environmental regulations demands a reduction in emissions.
Construction companies have found a way around this problem. Of all construction equipment in the United States today, 40 percent of units are rentals. If numbers continue to grow, predictions show that rental equipment utilization will surpass 50 percent in the coming years, and the logic behind this trend makes sense.
It’s often time-consuming and expensive for management to ensure their fleet is in full compliance. They can effectively outsource that anxiety by placing the responsibility on the rental service provider, trusting them to supply equipment that meets the standards of regulatory bodies. It’s a basic but effective strategy.
Despite the obvious benefits of renting equipment — like the elimination of maintenance and repair costs — rentals are more than a money-saving measure. They’re an intelligent method for managing a construction site’s carbon footprint, alleviating pressure on both the company and the environment as a whole.
3. Programs and employee training sessions
A construction company is more than its equipment. It’s a collection of trained laborers who coordinate on a site to bring a build to its final stages. The skills, abilities and experience of these individuals determine the success of a project in much the same way that they determine the project’s emissions and waste.
When a company implements programs and seminars to instruct its workforce, it can enforce the necessity of environmental compliance. As the workforce is taught the proper way to act in relation to equipment, waste management, spills and noncompliance events, they can achieve higher levels of efficiency and effectiveness.
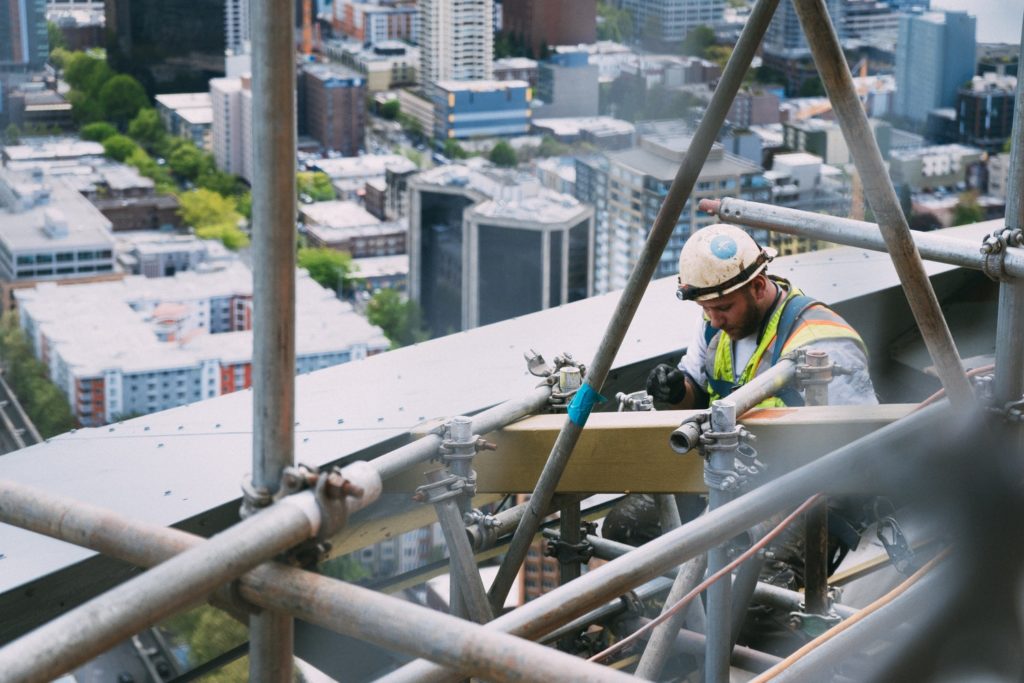
Construction companies are doing their part to preserve the environment. (Source)
For example, anti-idling initiatives can save money on fuel while reducing harmful emissions. Nitrogen oxides, particulate matter and toxic air pollutants are detrimental not only to the environment but also to the health of the workforce. Project managers can stress this point and others like it during a training session.
They can also train workers to recognize and report noncompliance in the field. When workers do so, a project manager can take action to resolve the problem. That said, cooperation is key, and it’s essential to equip these workers with spill kits so that they can attend to spilled materials before anything enters vulnerable waterways.
4. An opportunity for growth
The preservation of the planet is a shared responsibility, and construction companies are doing their part. Through environmental management systems, equipment rentals and employee training, the industry continues to reduce its carbon emissions and excessive waste, adapting to new challenges along the way.
As we move into the future, it’s safe to speculate that environmental regulations will tighten, constricting companies that are unwilling or unable to change. While this process might seem unsettling for some, business owners shouldn’t view compliance as an obstacle or obligation. Compliance is an opportunity for growth.
—
DISCLAIMER: This article expresses my own ideas and opinions. Any information I have shared are from sources that I believe to be reliable and accurate. I did not receive any financial compensation for writing this post, nor do I own any shares in any company I’ve mentioned. I encourage any reader to do their own diligent research first before making any investment decisions.

You must be logged in to post a comment Login