Business
Avoid these shipping pitfalls and improve profits
One little mistake in the label can lead to a big mistake for the company.
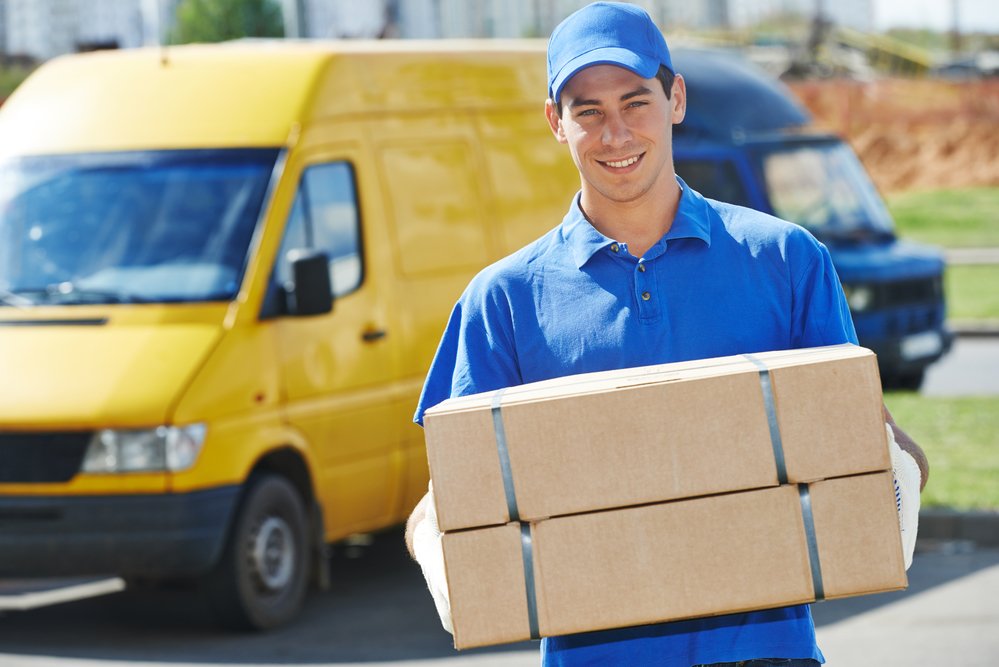
As all shipping industry professionals know, a lot goes into a successful shipping operation. With so many factors involved in the process, there’s a lot that can go wrong. Even small mistakes can lead to delays, smaller profit margins and less satisfied customers.
Being aware of these potential mistakes and putting extra effort into avoiding them is crucial to improving success. Here are some of the most common shipping pitfalls and how to avoid them.
Mislabeling shipments
Printing and affixing shipping labels are a central part of a logistics operation. It’s also one that’s easy to mess up. Even getting one number wrong in the address can send a shipment to the completely wrong place.
It’s easy to gloss over these mistakes, especially with so many numbers on so many labels flying through a facility. Encourage employees to watch for these mistakes because it will reduce their frequency. Using scanners can also help workers catch mislabeled packages.
Using the wrong packaging
You may want to just grab the first packaging option you see, especially if you’re in a hurry. But choosing the wrong one can lead to damaged goods. Packaging needs to be the right size and be able to support the weight of whatever it’s carrying.
A box becomes less stable even after just one shipment, so you should avoid reusing packaging. When choosing a size, make sure there is at least a couple of inches of room on each side once the object is in the box. This will help prevent cargo from damage.
Inaccurate class designations
It costs less to ship lower freight classes. Thus, shippers try to classify their shipments as the lowest designation possible. It’s important not to aim too low though because reclassification might lead to more fees. This could lead to delays as well. Carriers often inspect for freight class accuracy since it’s an important factor in how they make their money.
Improper loading practices
Even if you use the correct packaging, loading mistakes can still result in damaged goods. Lighter packages need to be placed above heavier packages so that they don’t get crushed. Workers must then properly secure everything, so packages don’t move around during transit.
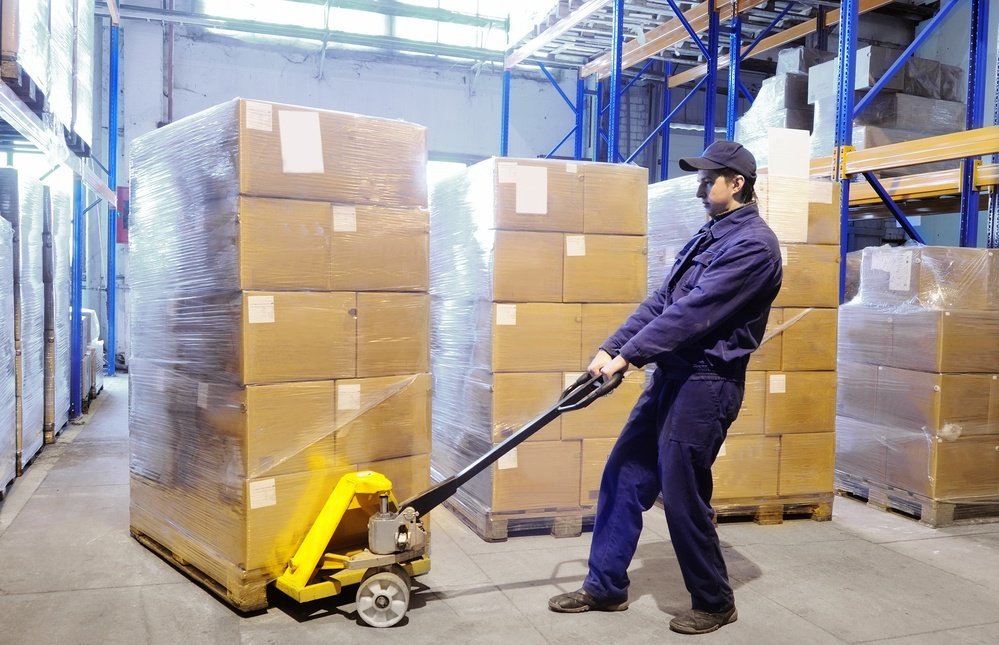
Heavier items should be placed below lighter items with parcels secured by a stretch wrap to avoid movements during shipping. (Source)
Most shippers now use stretch wrap to secure large loads to pallets because of its holding power and ease of use. Stretch wrap can expand to up to five times its original size without breaking, which allows it to wrap around all kinds of irregularly shaped items without damaging them.
Underestimating time requirements
In an effort to get products to customers as quickly as possible, some shippers may provide lower estimates for how much time workers need to load and unload freight. This provides faster shipping options to your clients but can lead to problems if your estimates are off.
Shipping delays lead to unhappy customers or worse, losing a customer. If a receiver has to work longer on your load than expected, this will cause delays, and they may charge you extra fees. It’s important to track load and unload times to make sure they are as efficient as possible. The key is to balance efficiency and employee safety.
Not notating damage
When a shipment arrives at any destination along its route, inspect and record any damage on the delivery receipt. Catching damage early enables you to repair minor damages before they get worse. If the damage is irreparable, you can replace the item quicker and avoid delays. If you notice damage but don’t notate it correctly, you may not recover your costs. The shipment would then have to be resent, effectively doubling your costs.
How improving shipping practices can increase profits
The mark of a good shipping operation is never making mistakes. It’s catching slipups before they cause more serious problems. There’s plenty that can go wrong during shipping, so it’s crucial to be attentive and deliberate in your processes.
Improve shipping practices will result in more satisfied customers and happier employees. It will also increase your profits. Mislabeling, inaccurate class designations and other mistakes can lead to extra fees that eat into profits. Improper packaging and loading can damage products and delay shipment. A more efficient and smooth operation will increase delivery times and help retain customers. It might even inspire them to recommend your services!
(Featured image via DepositPhotos)
—
DISCLAIMER: This article expresses my own ideas and opinions. Any information I have shared are from sources that I believe to be reliable and accurate. I did not receive any financial compensation for writing this post, nor do I own any shares in any company I’ve mentioned. I encourage any reader to do their own diligent research first before making any investment decisions.

-
Crypto1 week ago
The Crypto Market Rally Signals Possible Breakout Amid Political Support and Cautious Retail Sentiment
-
Crypto4 days ago
Bitcoin Hits New Highs in USD, But Euro Investors See Limited Gains
-
Crypto2 weeks ago
XRP vs. Litecoin: The Race for the Next Crypto ETF Heats Up
-
Crypto1 day ago
Crypto Markets Surge on Inflation Optimism and Rate Cut Hopes
You must be logged in to post a comment Login